A 25 años de la inauguración de su planta, General Motors Argentina avanza en
procesos productivos eficientes para acompañar las metas ambientales que se
fijaron a nivel global a partir del trabajo en alianza y la incorporación de nuevas
tecnologías.
Desde sus inicios como un típico campo argentino hasta convertirse en un referente en la industria automotriz, la Planta de Alvear de General Motors, en Santa Fe, recorrió un largo camino en su búsqueda por minimizar el impacto ambiental y mejorar sus procesos de producción.
El proceso de transformación comenzó en 1999, cuando la Planta sobre la ruta 9, se convirtió en la tercera de América en certificar la norma ISO 14.001, un hito que sentó las bases para la minimización de impactos ambientales y les permitió fijar objetivos de manera sistemática, planificada y documentada. “A partir de esta normativa toma relevancia la capacitación y comenzamos a transitar ese cambio cultural que se necesitaba para lograr objetivos a largo plazo”, detalla Norberto Tinazzo, Ingeniero Ambiental de GM Argentina.
Una de las primeras áreas en las que se enfocaron fue la gestión de residuos. Para llevarlo adelante, implementaron rigurosas auditorías mensuales en cada área, con objetivos de recuperación específicos, incluso incentivando la competencia entre equipos para lograr una disposición final adecuada. A lo largo de los años, y a partir de auditorías mensuales en cada cesto, se logró un gran aumento en la eficiencia de la separación en origen, pasando del 50% al 99,7% de residuos bien dispuestos actualmente.
El concepto de “landfill free” (libre de vertederos) se convirtió en una meta ambiciosa y, en 2008, se implementó con éxito en el sector de motores. Esta iniciativa se fue expandiendo
hasta abarcar todo el complejo en 2011, incluyendo a los proveedores, a los cuales se
los acompañó primero con capacitaciones y luego se generó un sistema de auditorías.
Desde la compañía explican que el éxito de la gestión de residuos, además de la capacitación y concientización de cada uno de los colaboradores, fue centralizarlo dentro del propio predio y no entregarlo a cooperativas o a terceros para su separación y comercialización.
“Fue una manera de visibilizar el valor que tenía eso que hasta hacía muy poquito era para todos basura –explica Tinazzo-. Por eso fue muy importante el proceso de identificación de cada elemento que antes se tiraba y establecer las 15 categorías con las cuales íbamos a trabajar”.
El proceso de ver el residuo como recurso los llevó de un predio a cielo abierto a la generación de una “eco-isla” que financiaron con el ingreso de la venta de todo lo reciclable. Hoy, es una planta productiva adicional en la que trabajan 25 personas en dos turnos y cobran en función de kilo separa-do. Por otro lado, se instaló un sistema de compostaje para los residuos vegetales para evitar que lo generado por los colaboradores terminara en vertederos.
La innovación se extendió más allá de la gestión de residuos y para lograrlo se basaron en la teoría del fin del tubo, corriente del pensamiento productivo-ambiental tradicional que se centra en buscar soluciones curativas una vez que los desechos y emisiones se han generado. “Hicimos el camino inverso y fuimos a donde se genera ese plástico, metal, madera, cartón, etc y trabajamos con el área de packaging y materiales para que a la hora de comprar tengan en cuenta el nivel de reciclado que tiene el packaging que utilizan, la maximización de piezas y el volumen por caja hasta la carga de los camiones para minimizar costos y por ende su huella”, detalla Tinazzo.
En paralelo al sector industrial se tomaron medidas en el comedor: reemplazo de los 1.5 millones de vasos plásticos por vasos de poli-carbonato lavables; se eliminaron las fundas de cubiertos y se colocaron dispenser de bebidas para evitar los envases pet.
Grandes desafíos
En esta línea, el complejo automotor de GM fue el primer parque industrial del país en certificar la Norma ISO 50.001 en materia de gestión eficiencia de energía. En 2020, el complejo recibió la premiación “Energy Star Challenge Award” por haber reducido un 10,4% el consumo de energía por vehículo en el periodo 2017 – 2019.
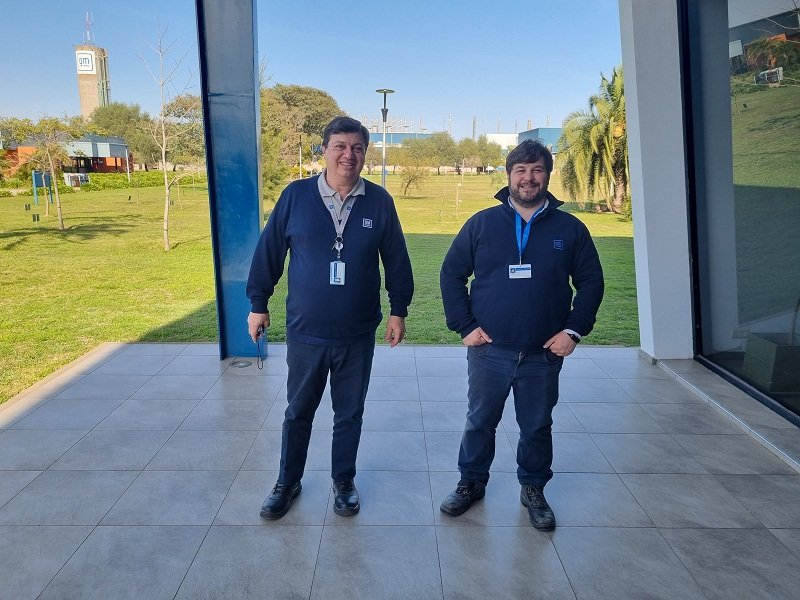
Asimismo, y con foco en el consumo eléctrico, se reemplazó recientemente el techo de la planta de motores para que sea totalmente translucido con luces dimerizables que, cuando hay sol, las luces bajan automáticamente su intensidad y viceversa logrando así un consumo variable.
Con una meta para el 2035 de utilizar 100% energías renovables la automotriz argentina recientemente instaló su parque solar de 400 paneles solares, que generará un total de 320 megavatios hogares en el mismo período. “Actualmente se logró cumplir con el 18% de esta meta ambiciosa. El parque solar ayudará a nivelar el 3% de su consumo anual total y estamos estudiamos constantemente el mercado para identificar las mejores inversiones”, explica Juan Ignacio Porta, coordinador de Mantenimiento en General Motors de Argentina.
La convivencia armónica de una empresa con un área protegida a una distancia menor de 500 metros constituye un desafío constante. “Nuestra Área Natural Protegida fue certificada por el Wildlife Habitat Council. Obtuvimos la categoría GOLD en términos de formación y educación en programas ambientales, situándonos en lo más alto”, cuenta orgulloso Tinazzo, además de haber sido finalistas entre las tres mejores instalaciones a nivel mundial.
Las capacitaciones ambientales internas son replicadas en la comunidad local a partir de charlas y talleres que brindan en colegios y universidades aliadas. “Volvemos a lo verde y mostramos cómo la empresa puede convivir con el área natural protegida”, afirma el referente de Argentina. Mientras tanto, en la automotriz continúan mirando hacia el futuro, trabajando en alianza con proveedores y gobiernos, explorando tecnologías y soluciones que
promuevan la sostenibilidad con caras a las metas fijadas a nivel global para el 2035.